4 min read
Top 4 Fastening Solutions for a Challenging Assembly Application
By: Benjamin Fischer Jun 29, 2022 8:15:00 AM
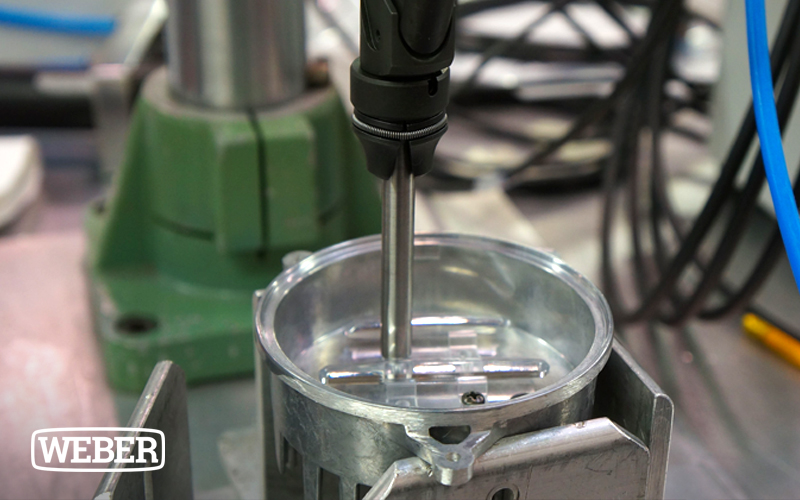
At WEBER, we understand that just because you have to solve a challenging assembly application doesn’t mean you need to resort to expensive, customized fastening solutions. Our automatic screwdriver and feeding systems make it possible to reach deep recesses, drive-in horizontal orientations, and adjust to situations where you need to register off the part to reach the active depth of an assembly every time.
Challenging assemblies include everything from organic shapes made from cast aluminum or plastic to composite materials and fixtured parts with different orientations. Optimal fastening solutions can integrate with your work cell to automate your assembly operation in the most difficult situations.
Solving Challenging Assembly Applications with WEBER Screwdriver and Feeding Systems
Automated screwdriver and feeding systems help you decrease cycle times, increase throughput, and reduce product liability. The following four systems are modular in design, meaning you can configure the system according to your needs.
Fixtured Vacuum Screwdriver
When the spindle cannot go all the way down to engage the screw on the part, we use a fixtured vacuum screwdriver to hold the fastener in place before we drive. This allows us to reach deep recesses or go aside an obstruction on the assembly.
The SEV system has a vacuum nosepiece and bit and makes it possible to access locations not usually possible with conventional screwdriver designs. It’s also a standard solution, meaning you can integrate it with a work cell, and you’ll always have parts available when needed.
The top features of the SEV system are:
-
Able to reach any orientation and can drive to inverted locations
-
Can accommodate almost any pneumatic or electric motor drive
-
Customizable nosepiece and bit components to accommodate different screw types
Vacuum Pick and Place Fastening Solution
In addition to the SEV system, we also have a vacuum pick and place solution when the application cannot use a feed tube to deliver the fastener to the screwdriver. The system still uses a vacuum spindle (the SEV) to drive the screw, but instead of running the screws through a tube, we deliver the fastener using a robot instead.
This design is ideal for applications where the fastener profile isn’t suitable to feed with a tube, so it increases the cycle time for each automated assembly. The part will sit in a dead nest before being picked up and moved to the spindle application.
Assemblies that Require Active Depth
A SEB configuration enables us to create a standoff on the nosepiece to register the active depth of a workpiece and ensure we drive to the required position. For parts where there are variations in dimensions, the active depth option on the SEB helps ensure that you achieve a flush drive every time using the reference of the actual part to calculate the required depth.
The SEB Fixtured Screwdrivers are designed to be used in a robotic application when the robot will bring the slide above the part, but the robot does not have a Z-axis fitted. The bit can be initiated to self advance its jaws stroke and bit stroke independently of each other for ultimate flexibility, which will also allow the device to advance forward, install a fastener while detecting the depth was achieved by both slides.
Long Stroke Vacuum Spindle
For long-reach applications that usually require you to hand-drive the screws, our LSCV Vacuum Spindle enables you to automate larger assembly operations. When you have a 3-inch-long screw that makes it challenging to transition the screw to the spindle, the LSCV vacuum spindle will hold the screw in the required orientation, giving you feed while you drive capabilities.
WEBER screwdriver and feeding Solutions for Any Challenging Assembly
We ask our customers to engage with us early so we can advise on part design and fastener selection to optimize the entire assembly process. This makes it easier to integrate the solution with your challenging assembly work cell and ensure a properly seated screw every time. Our C30 controller also measures in 3D (angle, torque, and depth) to highlight any quality issues with the assembly. If you need to solve a tricky fastening application using an automated screwdriving system, our team is ready to assist.
To see how our screwdriver and feeding solutions can assist in your challenging assembly applications, reach out to WEBER today.