3 min read
Minimizing Automotive Defects & Warranty Claims: Screwdriving & Joining Capabilities That Reduce Liability
By: Michael Rabasco Jan 30, 2024 9:00:00 AM
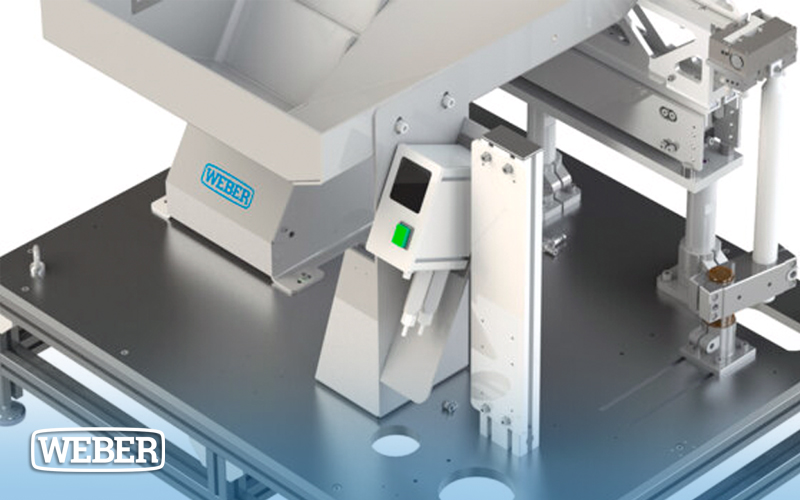
Automotive manufacturers must contend with increased liability concerns as safety devices and assemblies become more complex. From modern e-mobility vehicles to traditional internal combustion engines, manufacturers have to guarantee that each assembly meets the precise specifications and operates as designed.
To maintain the quality of each part, your screwdriving and joining capabilities should ensure you achieve the required clamp load during each assembly operation. To minimize product defects and avoid warranty claims, consider these proven screwdriving and feeding solutions from WEBER.
Error-Proof Automotive Assembly Operations with WEBER Screwdriving and Joining Capabilities
Eliminating errors during assembly operations of automotive components starts with developing an automated and repeatable screwdriving and joining process. WEBER’s screwdriving technologies provide the world’s automotive manufacturers with unparalleled capabilities that decrease cycle times, ensure consistent operations, and guarantee the quality of each joint.
How does WEBER get it right when others can’t? By deploying precise process control and capturing the data from each joining operation.
Controlling Screwdriving and Joining Operations for Reduced Liability Concerns
While WEBER’s screwdriving and feeding systems deliver precise and accurate assembly operations, the major difference comes from our process controllers. These are the Ferraris and McLarens of the screwdriving industry.
The C30 and C50 process controllers provide you with precise information about each joining operation. The controllers track the torque and angle (or rotation) of the spindle, but where WEBER’s systems smoke other options in the industry by tracking the depth of the fastener or screw during the process.
To be fair, it would be like pitting Lightning McQueen against Mater from the movie Cars.
The capability to track the precise depth of the screw during the driving operation will ensure you have zero defects in your automotive assemblies. If a joint doesn’t meet the specified clamp load, the programming on WEBER’s screwdriving process controllers will alert you and help you identify where something went wrong.
Problems that may occur include:
- Badly formed parts that prevent the fastener from reaching the required depth and torque specification
- Defective screws that made it into a batch and are shorter, smaller, or do not have the required coating or finish
- Pilot holes that aren’t up to standard and cause the screw or fastener to never reach the required torque at the specified depth
WEBER’s controllers will identify any of these issues and alert production staff to the problem. Instead of using secondary operations to perform quality validations, in-process data can ensure you never let a bad part leave the assembly line.
Because we use a tool-less design, operators can easily perform the required change-outs or services on the equipment. These joining and screwdriving capabilities reduce the cost of ownership, ensure each joint conforms to the requirements, and minimize liability concerns that lead to warranty claims.
Eliminate Errors in Automotive Assemblies with WEBER’s Process Controllers and Automated Screwdriving Technologies
We’re ready to help any automotive manufacturer and e-mobility producer that wants to error-proof their screwdriving and joining operations. WEBER has the expertise to identify where the biggest risks exist and how to manage them while ensuring shorter cycle times with increased uptimes and zero defective joints coming off the line.
To see how we can assist your automotive manufacturing operation, get in touch with WEBER today.