3 min read
Ensuring Safe and Efficient Assembly of Electric Vehicle Components with Advanced Screwdriving Systems
By: Carl Kulling Oct 3, 2023 9:36:00 AM
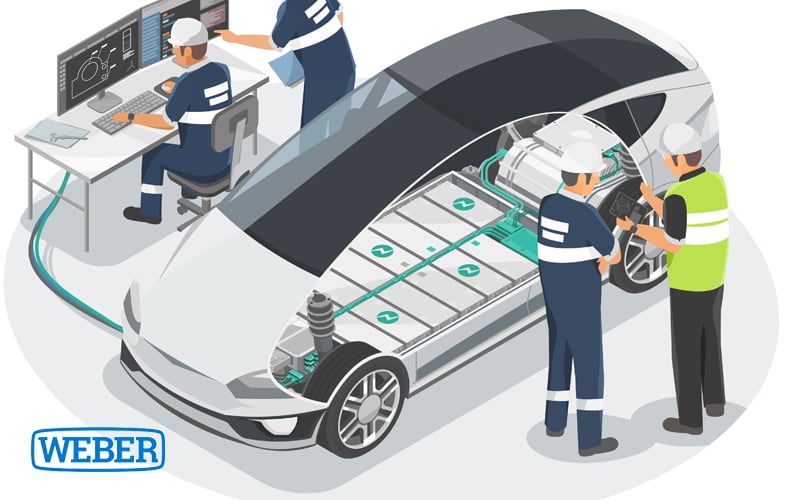
More drivers are transitioning to electric vehicles (EVs) year-on-year, as shown in the latest market analysis. In 2022, nearly 1 in 6 vehicles sold used electric drives and currently, the market is on track to account for 18% of total vehicle sales in 2023, according to research from the International Energy Association (IEA).
The industry is growing exponentially, with a 35% increase in sales between Q1 of 2022 and 2023. As more consumers opt for electric cars, manufacturers have to go through a similar transition when producing these EV components and parts. Although there are critical safety standards in all automotive applications, the additional concerns with high-voltage drives and dangerous current levels make the safe and efficient assembly of electrical vehicle components a critical function when producing these parts.
Advanced screwdriving systems play a vital role in ensuring part-to-part repeatability during the EV assembly process. In EV component manufacturing, the safety factors for each fastener may require tighter tolerances and demonstrable proof of compliance with more demanding technical specifications. In this blog, we’ll look at why EV component assemblies require stringent validation procedures in fastening and screwdriving applications, and how an automated solution can assist with improving both the reliability of the assembly and ensure greater operator safety.
Why EV Component Assembly Processes Carry More Risks
The automation journey became a necessity due to the stringent safety requirements needed to protect operators, ensure manufacturing reliability, and deliver a cost-effective production process that also reduces scrap rates by a significant percentage. During the initial development of EVs, there were many bottlenecks, quality concerns, and limited throughput in their assembly operations. By moving to automated assembly for crucial parts such as battery packs, chassis, and electrical drives, the company was able to drastically ramp up production of economically priced models every year and keep up with their rising consumer demand.
Some of the major hazardous operations in EV assembly operations include:
- Screwdriving high-voltage electrical components and battery packs without causing damage to the assemblies
- Handling the excessive torque required to drive the fasteners that ensure structural integrity
- Accurately driving screws and fasteners to the required depth, angle, and torque to avoid product liability concerns
Regulations struggled to keep up with major developments but as failure rates increased, a certain duty of care fell on the manufacturers of these critical components. Because of this self-regulation, ensuring product quality became non-negotiable.
How Advanced Automated Screwdriving Systems Became Essential
Steps taken during the pre-assembly preparation, sub-component assembly, the connection of battery-pack modules, and vehicle integration works that include wiring electrical components are becoming ever more complex. Maximizing output may require a screwdriving solution with an integrated feed system that can automatically stage, feed, and drive fasteners at less than a second per cycle.
These systems can handle the strenuous, repetitive operations that automotive assembly lines require while delivering unprecedented uptime and being rugged enough to handle the most challenging environments. With the right deployment of the technology, essential process data can notify production staff about a defective product, and allow root cause analysis to rectify the issue and prevent further production delays due to defects.
To error-proof your EV assembly line’s screwdriving operations, you’ll need:
- A fixtured screwdriving spindle that can operate from a base-mounted or robotically manipulated platform
- A feed system that delivers the next fastener to the spindle before the previous driving operation completes
- A process controller that can also handle data acquisition and generate a documentary record of each screwdriving operation
These advanced capabilities allow manufacturers of crucial electromechanical devices to error-proof their assembly lines and ensure zero failures while providing in-process quality validation during their screwdriving and fastening operations. WEBER’s advanced handheld and automated screwdriving systems, along with the auxiliary traceability solutions enable high-speed, accurate, and consistent operations when aiming for a profitable, but also safe and efficient assembly method for EV components.
Improve Safety and Traceability with WEBER’s Proven Screwdriving Systems in Your EV Assembly Operations
At WEBER, we work with manufacturers of EV components and parts to develop a fit-for-purpose screwdriving system. Our process controllers can measure the torque, angle, and depth of the screwdriving operation, providing you with accurate feedback that you’ve achieved your target clamp load every time. With quick-change tooling, configurable stroke lengths, vacuum technology for harder-to-reach applications, and process control that integrates with your Manufacturing Execution System (MES), you can deploy the most advanced screwdriving system that delivers the throughput you need.
Our team is ready to tackle your unique EV component assembly challenges. Reach out to discuss your application today.