4 min read
From Startup Assistance to Process Optimization: WEBER's Service Engineering Excellence
By: Michael Rabasco Nov 16, 2023 10:00:00 AM
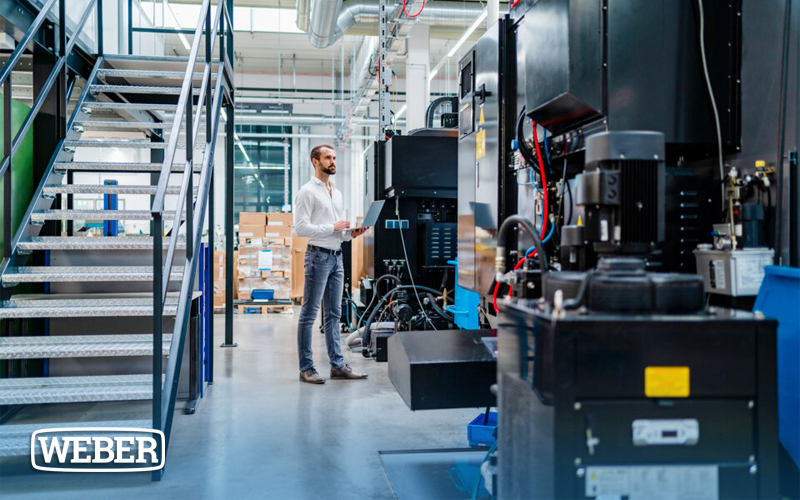
Industrial spending on automation is poised to increase considerably over the next few years. Many organizations will allocate as much as 25% of their capital budget to develop, implement, and optimize automation systems that can help improve output quality, uptime, and process efficiency. McKinsey’s research shows that 52% of assembly organizations are already on their automation journey, or likely to start one soon.
However, more than capital investments are needed to ensure the success of an automation growth strategy. Some key risks include the cost of hardware systems that solve the organization’s unique application challenges, and finding resources with sufficient skills to ensure the shortest pathway to productive growth. System design, build, and startup are only the first steps of the automation journey.
In automated screwdriving and joining operations, selecting a supplier that can guide, assist, and respond quickly is vital to any project’s success. Any shortcomings in these service engineering areas will cause delays, compromise reliability, and increase costs. Below, we look at how WEBER rises above our competitors to ensure you can implement an automated screwdriving system successfully.
Service Engineering Excellence from WEBER’s Joining Experts
Although WEBER is known for our rugged and reliable screwdriving systems, we also enable our customers to succeed with excellent after-sales service and support. These are areas where our competitors often lack the necessary expertise that a successful automated screwdriving system implementation depends on.
To ensure a successful implementation, we have three main categories of service engineering available to our customers.
Startup Assistance
The initial startup process of the screwdriving system is often where things start to go wrong. While the sequence of operations, the application parameters, and the cycle times will determine the automated screwdriving system design, it’s when you have to bring all of these elements together to run perfectly in sequence that you may need additional assistance.
During startup assistance, a WEBER technician will help you iron out any bugs and validate that the system is working as required. Working with your operators and your on-site engineers, WEBER’s joining experts will guide your resources to make the adjustments for small variations where required.
Process Optimization
Process optimization looks beyond WEBER’s screwdriving system to evaluate the entire assembly process for improved reliability. A myriad of factors could influence the repeatability, accuracy, and consistency of your screwdriving and joining operations.
Poor quality fasteners and parts could lead to compromised joints that increase product liability. With WEBER’s control systems, you can specify the exact torque, angle, and depth parameters for each automated screwdriving operation. When a driving operation fails to achieve the specified results, the system will alert you that something is wrong. These error codes will help you understand where the process issue originates, and our service engineers can recommend the required changes.
Ongoing Training and Support
While WEBER’s joining experts are always available to help you if something goes wrong, we also provide training and support for your own resources. By having a qualified technician available at your facility, you can reduce any downtime by quickly troubleshooting the issue and taking corrective actions in-house.
WEBER’s experts will be available to these resources if they need additional assistance and will guide them through any scenario to identify, understand, and correct the error. All of the documentation required to ensure reliable operations are shipped with WEBER’s screwdriving systems, giving your team the tools they need to maximize your assembly line’s uptime.
Speed Up Your Automation Journey with Service Engineering Support from WEBER’s Joining Experts
WEBER has the technical resources available to help you optimize your entire automated screwdriving and joining process for unmatched reliability. With our dedicated service and support offerings, you can trust WEBER to help get your automated screwdriving system dialed in and operating exactly as designed.
You can deploy WEBER’s solutions to maximize your throughput, improve your OEE, and deliver quality output repeatedly. Our joining engineers are backed by a team of experts with decades of industry experience which gives you access to the world’s leading automated screwdriving technologies.
If you are starting your journey towards automated screwdriving operations, contact WEBER to find out how our startup assistance services and joining engineers can assist you today.