4 min read
Error-Proofing Screwdriving and Ensuring Compliance For Aircraft Component Assembly - Part 2
By: Tom Ash Feb 21, 2024 8:30:00 AM
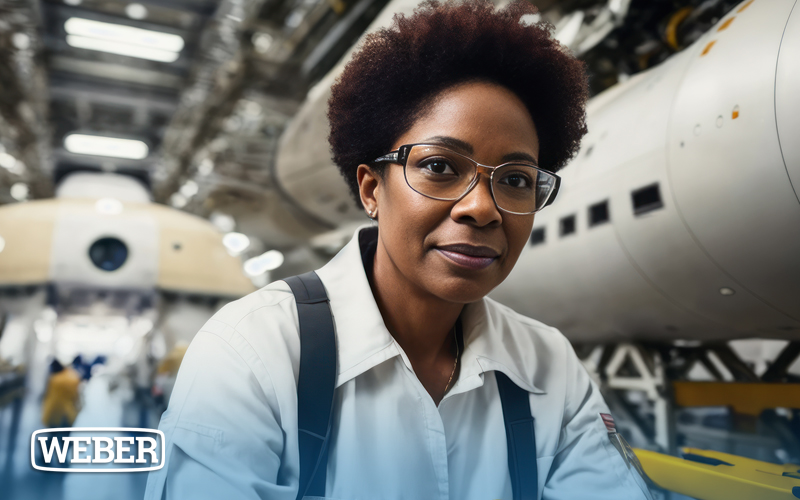
Following on from our previous blog about how to set up an automated, repeatable, and consistent screwdriving process, in this post we’ll explain how to mistake-proof your assembly line.
This is the second blog of a two-part series discussing how to error-proof your automated screwdriving process and eliminate all failures from the assembly line.
Mistake-proofing, Poke-Yoke, or fail-safing are terms used to describe an automated method that makes it impossible for an error to occur during the manufacturing process. The methodology originated from Shigeo Shingo while working at Toyota, but it’s a standard process analysis tool used in many manufacturing environments today.
The mistake-proofing process usually includes the following 3 steps:
Identifying areas where errors may potentially occur
Establishing controls to detect errors during the assembly process
Using sensors to monitor the process and gather data to demonstrate zero failures
In screwdriving applications for aircraft assemblies, error-proofing requires manufacturers to verify that each driving operation achieved the specified clamp load. Driving to the right depth with the correct torque and angle will ensure that each joint operates as designed.
Controlling the Screwdriving Process with Precise Load Parameters
To ensure the proper seating of each screw, a process controller will execute the operation according to your precise specifications. The driver and torque transducer uses WEBER’s C30S process controller to drive the screw to the correct position using an analog depth sensor, at the required angle and within the precise torque requirements.
The C30S comes with pre-loaded screwdriving applications and a programmable interface to develop any screwdriving program to suit your requirements. Because the system interfaces with your PLC, it will initiate the bit and stroke only once it receives the corresponding signal from the Manufacturing Execution System (MES), and communicate with the PLC after the operation completes. You can maintain a steady, predictable, and repeatable index of aircraft assemblies on your line to maximize your production capacity.
A 3D screwdriving process controller from WEBER will:
- Ensure consistent and repeatable screwdriving operations according to your design parameters
- Control the angle, torque, and depth of the screw being driven to guarantee you achieve the required clamp load on the assembly
- Detect any deviations and alert the MES to any issues where the required screwdriving parameters have not been met
Precise process control is how you can error-proof your automated screwdriving tasks. The system will alert when the angle over-ran its specification, where the torque was over or under during driving, and monitor the depth of the screw where these events occurred. Because it interfaces with your PLC, you can incorporate in-line process validation and stop the line when an issue arises.
Gather Process Data and Demonstrate Compliance
To demonstrate compliance, you should gather the required process data and performance parameters for each screwdriving procedure. This data provides proof that the joint achieved the required torque, angle, and depth as per the specification.
Because you are stopping any defective components or assemblies from coming off the line, you can also track your overall performance and continue making corrective adjustments to the process for improved quality. Integration with your MES and QMS systems allows you to document each screwdriving process and deliver these quality records to your customers to easily demonstrate compliance.
By gathering process data for each event, you can:
- Certify each joint meets the required clamp according to the aircraft assembly’s design requirements
- Keep records of all parts that you produce and investigate any failures discovered in a joint quickly
- Continue improving your process by adjusting the screwdriving strategy, optimizing part geometry, and monitoring overall production speeds
With automated screwdriving solutions from WEBER, you can eliminate errors from your production line and increase profitability. We can help you calculate the ROI available from screwdriving automation in this eBook to see how decreasing labor dependency will establish a more resilient manufacturing operation.
Eliminate Errors from Your Screwdriving Assemblies with Intelligent Control from WEBER
WEBER makes automation (and error detection) easy with our intelligent process controllers. You can speed up production without increasing product liability risks, and verify that each fastener or screw achieved the required clamp load. If any errors do occur, you can analyze the performance data to find the root cause of the problem and take corrective actions quickly.
With an automated screwdriving system from WEBER, you can rest assured that each joint coming off your assembly line meets the required specification parameters.
Download our latest eBook here if you want to learn more about our automation solutions and screwdriving systems.