3 min read
Enhance Reliability in Manual Subassembly Tasks with Automated Screwdriving Technology
By: Michael Rabasco Jan 9, 2024 9:00:00 AM
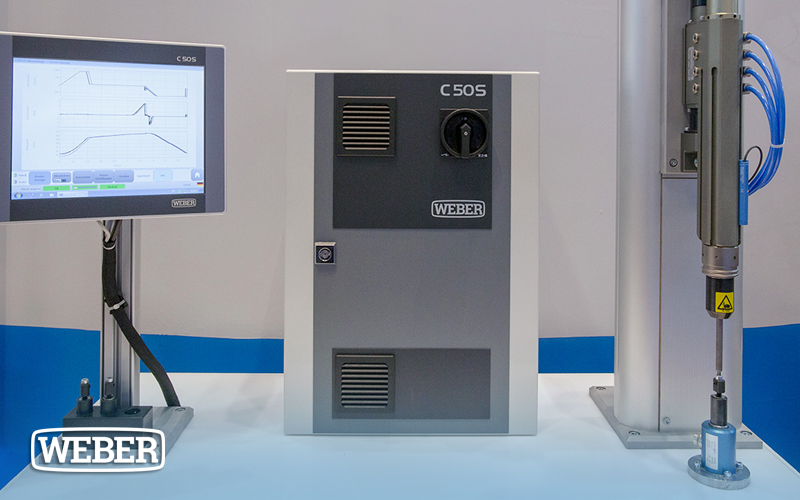
Whether you are assembling 3 parts to complete a fuel transfer pump or putting together a speaker, manual subassembly tasks could lead to reliability concerns that increase product liability risks. When you have to accommodate a human element in the assembly process, factors like consistency, repeatability, and overall quality may fall by the wayside even if it's unintentional. Most of this is due to the lack of traceable error-proofing.
Along with the quality concerns that manual (by hand) assembly brings, most manufacturers must contend with decreasing labor participation rates across the industrial sector. Operators and technicians are becoming scarcer, forcing manufacturers to consider fully automated solutions.
WEBER offers automated screwdriving systems that can handle any application where repeatability, consistency, and speed are required. Compared to other solutions, our screwdriving solutions are accurate, fast, and easy to operate.
Our screwdriving technology can deliver the consistency you need as part of an automated process while improving safety on the assembly line. To enhance the reliability of your automated subassembly tasks, consider these automated screwdriving technologies from WEBER.
Reduce Quality Risks in your current Manual Subassembly process with Automated Screwdriving Technology
Establishing a screwdriving process for manual subassembly requires extensive experience in human and machine interactions. The pneumatic plan and sequence of operations have to be fully understood before you can error-proof and Poke-Yoke the process.
Whenever humans are involved in a subassembly task, there is a risk of error creeping into the process. To Poke-Yoke a subassembly screwdriving operation, manufacturers have to:
- Identify any steps in the sequence where there is a risk of human error
- Develop automated controls that reduce the risk of error or make errors obvious
- Deploy automated inspections and validations to ensure zero errors coming off the line
Along with WEBER’s automated screwdriving and feeding technologies, we also provide process controllers that perform validations for each screw’s angle, torque, and depth.
With subassemblies, knowing that each screw achieved the required clamp load is essential to limit the risk of product failures. WEBER also has decades of experience in assisting firms to Design for Automation. This could include reducing the different types of screws you use in assemblies, making small changes to the part’s geometry, or including female/male divots to ensure the correct alignment of two pieces when fixturing them on the assembly cell.
WEBER’s Process Controllers for Zero-Error Manual Subassembly Tasks
An error-proof process will depend on the automated screwdriving solution that gathers data about each driving operation. Depending on the complexity of the subassembly and the regulatory frameworks involved, having this data available will also reduce the cost of compliance.
WEBER’s C30 and C50 process controllers can:
- Measure the torque, angle, and depth of each driving operation
- Interface with other Manufacturing Execution Systems (MES) via open interfaces (Profibus, Profinet, Ethernet, and Digital)
- Generate and document performance results for record-keeping and demonstrable compliance with each assembly’s process parameters
The C50 also monitors gradient torque to provide detailed records of the rate of change between torque, angle, and depth parameters. By monitoring this information, you can ensure you consistently achieve the required clamp load at the specified depth of the subassembly’s specifications.
Establish an Error-Proof Screwdriving Process with WEBER Technology
WEBER solves complex screwdriving applications for subassembly tasks where humans and machines have to interface during operations. The robust and reliable screwdrivers and feeders will maximize your uptime while our process controllers maintain the required quality.
With labor participation rates down, demand for assemblies increasing, and the cost of compliance rising, you can deploy an automated screwdriving solution that solves your daily challenges.
To find out more about WEBER’s screwdriving and feeding solutions, speak to one of our joining experts by contacting us here.