1 min read
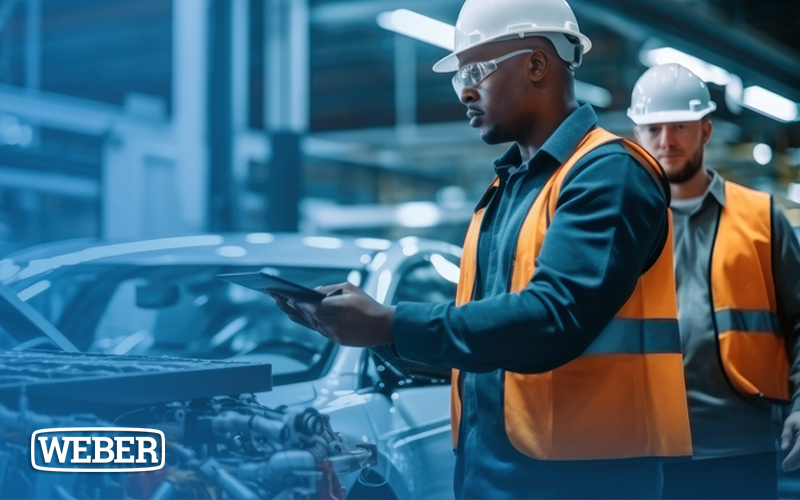
Subscribe to stay up-to-date on our latest news and educational content!
By: Michael Rabasco Apr 10, 2024 9:30:00 AM
To ensure the proper installation of each fastener, manufacturers need to monitor the angle, torque, and depth of each driving operation. The combination of these process parameters will indicate when a part or screw didn’t meet the required quality by either torquing too high early in the driving process or never reaching the required torque at the specified depth.
WEBER’s process controllers use a torque transducer to monitor any spikes in torque or angle in the screwdriving process as well monitoring the precise depth the screw is as it is installed. The controller can then send that data l to the MES to validate the assembly process. By collecting the process data, manufacturers can investigate issues that lead to higher scrap rates and take corrective actions to ensure part-to-part repeatability
WEBER’s process controllers provide precise monitoring and control of each screwdriving operation. The controller can integrate with PLCs, initiating the driving operation upon receiving the start signal. Measuring the torque, angle, and depth of the driving operation is possible using the analog depth sensor and transducer in the spindle. The C30S process controller also controls the feeding system, the stroke movement of the spindle, and can communicate with other peripheral devices.