4 min read
Tips for Selecting the Right Screwdriving Assembly Method for Your Product & Facility
By: Dan Brzezinski Sep 20, 2023 9:35:00 AM
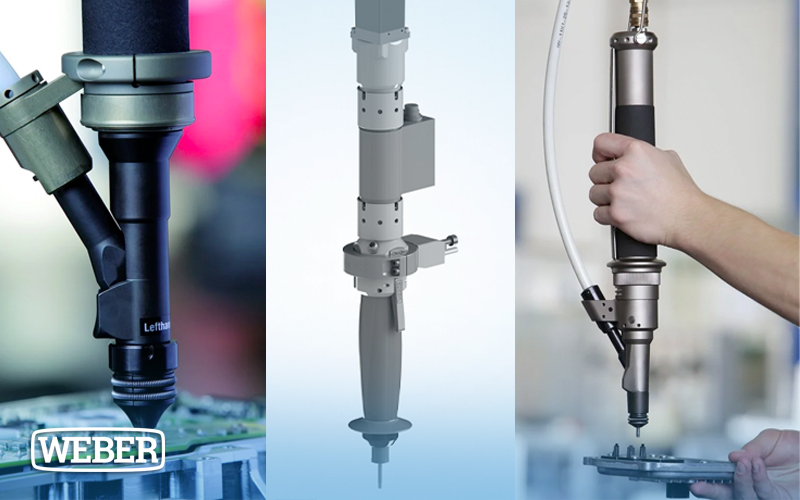
Keeping up with production rate demands in today’s hamstrung manufacturing sector is pushing many producers to the brink. Finding talent, maintaining quality output, and delivering on schedule requires a strategic rethink of your process to secure your margins and lay the foundations for continued growth.
Selecting the right screwdriving assembly method can help manufacturers overcome the challenges of today, and set up a production process that can scale with increased demand. Screwdriving and fastening operations often dictate the pace of the manufacturing line, making the methodology you use a key factor that affects your overall productivity. With a variety of approaches, technologies, and solutions available, let’s discuss what you should look for when selecting a screwdriving method for your assembly operations.
3 Tips for Selecting the Right Screwdriving Assembly Method
The key trends driving the manufacturing sector in 2023 mainly aim to overcome the challenges that emerged over the last few years. Investments in skills development, automation technology, and organizational sustainability dominate the strategic playbooks of today’s manufacturers. Any solution you choose should meet these goals, and unlock additional value for the organization wherever possible. Here are three tips for choosing a screwdriving assembly method that will provide a positive contribution to your bottom line.
Improving Cycle Times
Any improvement in the cycle time of your current screwdriving assembly process will have an immediate impact on your productivity. Whether you have a manual process or use a semi-automated screwdriving solution, the rate at which you feed and drive each fastener determines your overall output for each shift.
A solution that can feed while you drive will drastically shorten your cycle times. WEBER’s pneumatic and electric screwdrivers deliver the fastest cycle times by integrating a swivel arm feed head onto the driver. This allows you to feed the next fastener during the current screwdriving operation, allowing you to start a new drive cycle as soon as the previous one is finished. This will allow you to achieve higher output goals as demand increases.
Reducing Labor Dependency
If your output depends on human operators, you could be putting your schedule at risk. Employees take breaks, go on leave, or call in sick. You may also struggle to find a replacement if an employee leaves, as there are almost 800,000 manufacturing jobs currently unfulfilled.
Making strategic investments into automation now can help you reduce your dependency on human operators, allowing you to scale operations to meet future demand. WEBER provides fixtured screwdriving systems that deliver fully automated assembly operations, including the bulk feeding of screws with minimal operator intervention required. These solutions are tailored to your specific application, and with our vacuum technology, can overcome any assembly challenges such as driving into an area with very restricted access.
Ensuring Quality Output
In-process validation and error detection are critical procedures in screwdriving assembly operations. If fasteners do not reach the required clamp load, you risk bad products reaching your customers. While product liability will differ across different applications, too many out-of-the-box failures will tarnish your reputation.
With WEBER, you can establish in-process validation using our C30S controllers. The controller manages the entire driving operation and gathers critical process data about the torque, angle, and depth of each fastener you drive. This information helps you to detect issues with parts and screws and provides demonstrable proof that the assembly meets the design specifications. The analog depth sensor is accurate to ¼ of a millimeter, giving you the most accurate indication that you’ve reached the required depth, at the torque and angle specification required.
Future Proof Your Screwdriving Assembly Method with WEBER
WEBER delivers where other screwdriving manufacturers can’t. Our systems are rugged and reliable, capable of driving millions of screws per year with limited downtime and operator involvement. The feed systems can handle most kinds of fasteners, even where the dimensions make it difficult to feed or maintain the correct orientation at the escapement.
With WEBER, you can make automation easy and secure your future scalability without increasing your labor dependency.
To discuss your screwdriving assembly methods with an expert, get in touch here.