4 min read
SBM25: Insertion System for Blind Rivet Nuts and Bolts
By: Michael Rabasco Jul 9, 2024 9:00:00 AM
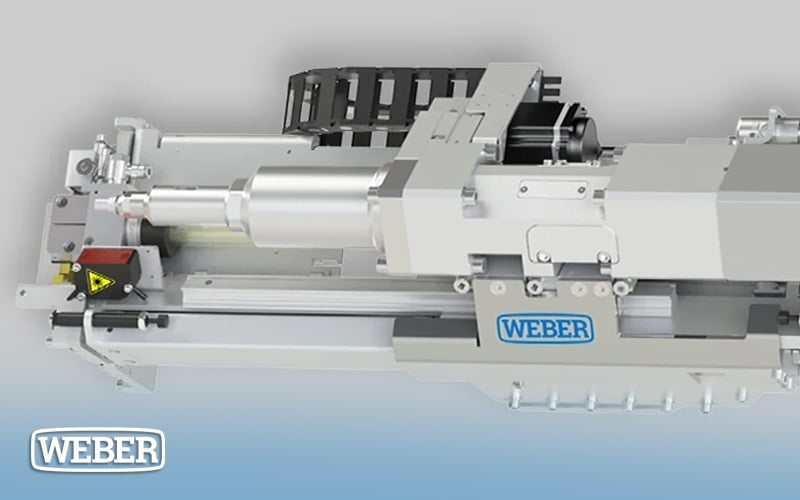
The WEBER SBM25 Insertion System for Blind Rivet Nuts and Bolts eliminates the headaches that come with installing blind rivet nuts and bolts in the assembly industry, most notably for the automotive industry and for EV battery assembly operations. Once in production, you will have laser-guided alignment for installing cylindrical and hexagonal shanks up to 25 kN, you will receive detailed production data analytics, and you may never have to change out a mandrel during production again.
What Can the SBM25 Do For Your Operation?
In a production environment, the SBM25 is an autonomous, continuous-feeding system with a docking-capable interface that requires little attention. It automatically loads a rivet nut from a step feeder and carries it through a piece of tubing that's 20, 30, 40, or even 50 feet long and loads it into a gun. The gun moves forward and in the case of a hexagonal rivet, it slowly rotates the rivet nut using lasers to calculate the position of the hex radially. Then, the gun slip-fits the rivet nut perfectly into a pre-cut hole. A mandrel is then inserted into the rivet nut to the correct depth and then pulled to set it. All of this is without human intervention.
Got Mandrels? No Problem
Tracking and replacing mandrels is one of the biggest headaches in the spin-pull process. Inserting, pulling, and unthreading during each cycle subjects mandrels to wear and tear, and their shelf life limits the number of cycles where they can reliably perform.
Mandrels can be a pain, the are both time consuming and difficult to replace when the mandrel is worn, it can break inside of an assembly or spindle. It can bind up in a part and jam the entire system up and be very difficult to remove. However, the SBM25 tracks the number of cycles a mandrel has performed and monitors its wear and tear. When the controller senses that the mandrel is weakening or it reaches a preset count, that mandrel is replaced automatically and discarded without any human intervention by a machine technician or operator This is a truly unique feature that saves machine process downtime because the mandrel exchange can generally happen between part loads so as to have no impact on overall system throughput. WEBER can also supply a mandrel feeding and nesting system that can hold hundreds of mandrels and completely automate the mandrel exchange process to ensure hands off operation shift after shift.
Or an operator can simply load a simple magazine with mandrels at the beginning of each shift, and the SBM25 will autonomously change the bit when it's time and drop the old one into a garbage can. No alarms, no one gets called, and downtime is avoided and production never stops.
Traceability For Blind Rivet Installation
Problems can easily occur during blind rivet installation on a production assembly line. During manual installation, a mandrel may not be inserted to the correct depth, or something may be wrong with the materials causing the blind rivet nut to not set correctly. When that happens, insufficient expansion or clamping force can result in loose joints that can slip, loosen, or fail, which can be a big problem if product liability or safety issues are involved.
That's why feedback is critical during blind rivet installation because feedback and traceability can tell you how well each rivet was installed. The controller monitors the amount of pulling force and the distance traveled during each upset so that you know that each and every blind rivet installation concludes with a good set. Everything is tight and where it needs to be. Data for any failed setting processes (NOK) can be interrogated through the controller fault log for identification root cause analysis ensuring continuing process improvements are easily identified
Download WEBER's latest brochure entitled Setting System for Blind Rivet Nuts and Bolts SBM25 to learn more about the many features of the SMB25.
More Features
Here are a few more innovative product features of the SBM25:
- The mandrel is spring-loaded to prevent damage to the thread during insertion and removal, an area where we found some of the mandrel wear comes from.
- The mandrel will be automatically changed based on how many cycles it completes, predicting when it will be worn out. This means more up-time and predictable but limited downtime
- This durable system is optimized for more than seven million cycles, even at maximum load.
- The latest generation of IT security and control technology is included.
- Automation-friendly cycle times from five seconds are possible.
- The process is stable regardless of position in any working direction, and it can feed or set in any direction.
- A dockable spindle system allows for alternating different sizes or types of nuts and bolts.