4 min read
How to Avoid Screwdriving Integration Issues Within an Assembly Operation
By: Tom Ash Mar 7, 2022 8:15:00 AM
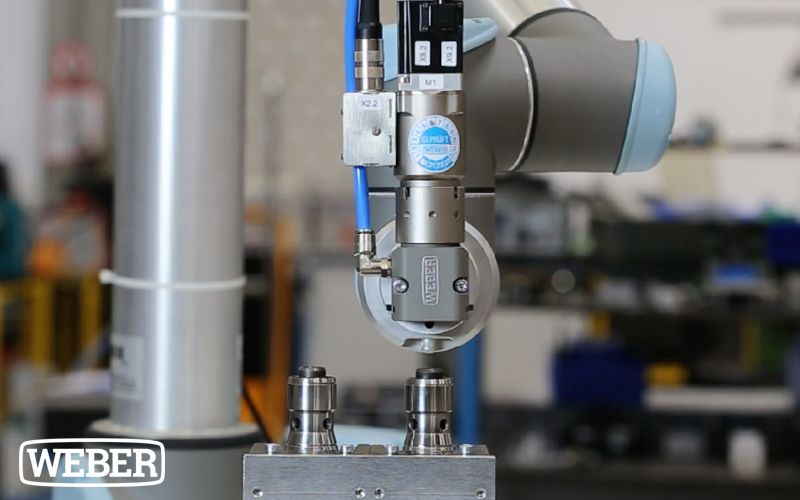
Integrating an automatic screwdriving system within a machine cell & overall assembly operation can be a major challenge for machine builders. Any breakdown in communication between the end-user and system supplier could lead to downstream product liability issues.
Designing the system correctly from the start will be key to avoiding issues that could cause a product recall, which is exactly what happened with some Porsche Taycan models in 2021. To ensure you can drive each screw correctly and validate the entire process, there are some practical considerations to keep in mind.
In this blog, we’ll look at some of the biggest challenges machine builders need to overcome when integrating automatic screwdriving systems with assembly operations.
3 Best Practices to Avoid Screwdriving System Integration Issues in Assembly Operations
Successfully automating your screwdriving operations is a complex process. At WEBER, we know that automation isn’t simple, and we’ve seen many projects run into production issues if you don’t follow the right approach from the start.
Major challenges that engineers need to overcome with automatic screwdriving include:
- Available space – The fastening station will need to operate reliably within the available space on the production line
- Fastener type – The type of fasteners used may determine the type of feeding system and cycle rates that you can maintain during automatic screwdriving
- Product complexity – Some applications need to maintain cleanroom conditions and reduce particulate build-up that could lead to quality issues
- Process control – Engineers will need a feedback system that provides the required data to validate the process and help with fault analysis
Below, we discuss three best practices to follow when starting an integration project for an automatic screwdriving system.
Document the Exact Requirements
Documenting the requirements early and accurately ensures the system can perform as per the end user’s expectations. This will also highlight any additional design considerations required to configure the system that will be vital information for the supplier. Before you engage with a screwdriving system supplier, gather details about:
- Required cycle times and expected availability to maintain the necessary production quantities
- Precise process specifications for each driving operation including the angle, depth, and torque requirements
- Review the latest product drawings to understand any special screwdriving considerations such as available clearances for screw access and space constraints in your proposed work cell.
- Description of the process control functionality needed to assist with identifying problems and validate each screwdriving operation
Evaluate Your Potential Suppliers
The selection of the vendor will likely be the most important part of the process. Your supplier should provide you with engineering support during the entire process and alert you to any common pitfalls in mechanical fastening operations that you may have missed.
Look for suppliers that:
- Provide modular system designs making it easier to configure a solution suited to your application
- Provide ongoing services and support for the automatic screwdriving system including the availability of replacement parts
- Can validate the system design with metrics and analytics such as Mean-Time-Between-Failure (MTBF) and Mean-Time-To-Repair (MTTR)
Look for Value-Added Services
Along with engineering support, some solutions can assist with identifying process quality issues early. The controller for the screwdriving operation should record data about the angle, torque, and depth of each screwdriving operation. This will help with quality assurance and root cause analysis when a failure occurs.
Ask your supplier if:
- They provide detailed documentation including the sequence of operations and schematics to assist with ease of system integration
- The system controller can gather and export multidimensional performance data for every screwdriving operation that helps validate the process
- It’s possible to build in optional vision systems to avoid feeding the wrong fastener to the driver and prevent quality issues before they happen
Avoid Integration Issues With Automatic Screwdriving Systems From WEBER
WEBER works with the world’s leading manufacturers to eliminate quality issues and maintain system reliability during assembly operations. Our solutions come in standard, modular designs that you can configure for any automatic screwdriving application. We can assist machine builders to configure the ideal system that performs according to the end-user requirements and provides additional quality assurance data about each screwdriving operation.
To discuss your screwdriving integration requirements with a team of experts, get in touch with WEBER today.