1 min read
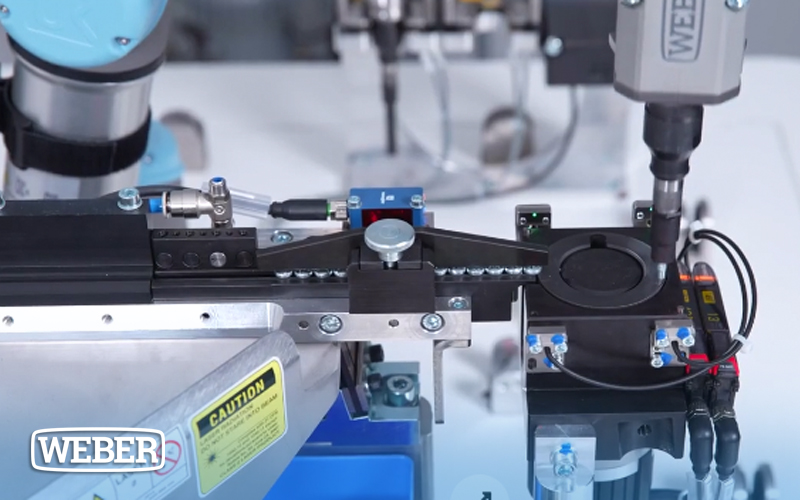
Subscribe to stay up-to-date on our latest news and educational content!
By: Michael Rabasco Apr 29, 2024 2:05:46 PM
In our experience, two factors can make seating your screws to the required specification in a challenging assembly untenable. The first is poor quality parts coming down the production line and the second is a bad assembly design. In these situations, WEBER can still overcome many of the challenges by helping with error recognition or by tailoring our solutions to fit within your design constraints.
Preventing product failures, especially before they reach the end-user, is critical when automating your screwdriving operations. If an airbag fails to deploy correctly due to an unseated screw, the liability you face can be astronomical. The same applies if an accident avoidance system vibrates loose and takes out the sophisticated electronics that modern vehicles and consumers depend on.
A custom screwdriving system can assist you with error-proofing the line and help maintain the shortest possible cycle time while adhering to the laws of physics. The three main challenging assembly applications most frequently encountered are: