Feeding screws that have a shorter thread profile than the dimensions of the head present a challenge to automated assembly operations. Maintaining the required orientation in the feed tube isn’t possible when the length and breadth of the fastener don’t provide a distinct profile and may tumble in a round feeding hose. In these situations, there are only three viable options available to engineers.
Check out this video or keep reading to learn more:
- You can change the profile of the screw by making the shank longer or the head smaller
- use a profiled feeding tube
- opt for a WEBER pick-and-place screwdriving solution
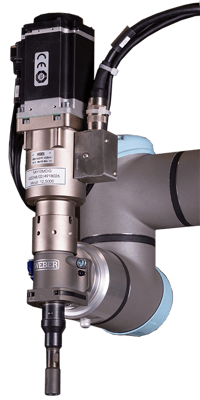
The second option allows you to feed the screw into a profiled tube and blow it to the driver in the right orientation, but this approach increases the cost, and you’ll need to ensure the screw manufacturers adhere to your tighter tolerances.
Finally, you can opt for a pick-and-place system where you present individual screws to the driver using a robot. The system uses a vacuum spindle (the SEV) to drive the screw, but instead of running the screws through a tube, we deliver the fastener using a robot. This design is ideal for applications where the fastener profile isn’t suitable to feed with a tube, but it increases the cycle time for each automated assembly. The part will sit in a dead nest before being picked up and moved to the spindle application.
By engaging with WEBER early in the design process, we help you find an optimized solution that can save you plenty of headaches down the line.